Michigan State University Uses DLP to Improve Metal Additive Manufacturing
Joel Coffman2023-10-26T12:39:30+00:003D printing began as a tool for rapid prototyping, and it has been evolving within a variety of different technologies. As this process is beginning to be utilized more often in additive manufacturing, the 3D printing of metal parts has become more popular. Hoa Nguyen and his team of researchers in the Michigan State University Lab of Advanced Manufacturing Processes have been studying how to improve conventional and additive manufacturing processes. Their most recent publication in CIRP Annals – Manufacturing Technology tackles the current cost and size issues that are being faced in today’s metal additive manufacturing technologies. The MSU team decided to design a prototype that uses DLP (Digital Light Processing) technology to develop an innovative and more affordable metal additive manufacturing process.
The current metal 3D printing technologies are limited by curing depth, high costs, and a small scale suited for low production. The process to successfully fabricate metal through additive manufacturing consists of the photopolymerization of an ultraviolet (UV) curable metallic powder suspension. In order to hold the metal particles together, the photopolymer is selectively cured from liquid to solid state. The final product is then achieved by subjecting the resin metal matrix to appropriate thermal treatments.
By using DLi’s 3DLP9000 405nm Light Engine, Nguyen’s team was able to construct a prototype that allowed for an increase in the build plate size without losing dimensional accuracy and a decrease in the single layer print time. Check out the image gallery below for a look at the MSU prototype.

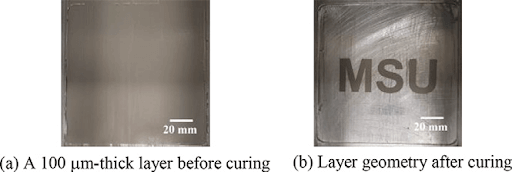


Overall, this new, metal SLA-based (stereolithography-based) additive manufacturing process has some superior advantages to other metal 3D printing technologies. With a DLP projector system in place, the MSU team created a new additive manufacturing process with improved accuracy, fabrication speed, and scalability. Additionally, in comparison to a galvo-laser system, their final prototype has shown to be relatively inexpensive by using the 3DLP9000 Light Engine as their DLP projector system.
Click the Read More button below for the full paper, entitled “Development of an innovative, high speed, large-scaled, and affordable metal additive manufacturing process,” on ScienceDirect.com.